We all love having products and features in our lives that make the day just a little bit easier, safer and more enjoyable. However, it is becoming apparent that we must keep the health of ourselves and our planet at the forefront of our design process. Increased drought frequency, heat waves and other extreme weather events are becoming more common around the world. There can be no question that the mere act of manufacturing a new product can contribute to these problems. So, what can we as manufacturers and consumers do about it?
Choose products that improve our lives while also providing a benefit for the environment
Every manufactured good has a life cycle that starts with raw material extraction and ends with disposal. As consumers, it is hard to know what that lifecycle actually entails since every manufacturer has a different supply, production and sales pipeline. The key lifecycle stages that contribute to a product’s environmental impact are: raw material sourcing, production, distribution, operation and disposal. To minimize the impact of a product there are many variables to take into account within each lifecycle stage.
Raw material sourcing
Raw material sourcing is one of the most challenging phases for a manufacturer. It often involves an interplay between selecting the best material for the task while balancing cost and environmental responsibility. For example, some materials may be more recyclable and machinable but may cost more money or require longer shipping distances. Plumbing fixtures interact with our drinking water and are subject to high material standards. Requirements for low lead content limit the alloys of brass that can be used and harmful substances such as Bisphenol A (BPA) that can be found in many plastics can cause harm. To this end, it is imperative that a manufacturer know what is in each component of a plumbing assembly and be able to certify that it is free of harmful contaminants.
Certifications from the NSF, CSA and UL help consumers determine if a product has gone through a rigorous 3rd party audit to ensure its safety. The next time you are buying a plumbing fixture ensure that it complies with NSF/ANSI 61 drinking water standards as well as is certified low-lead by CSA or UL as indicated by the “LLC” initialism on the approver’s label.
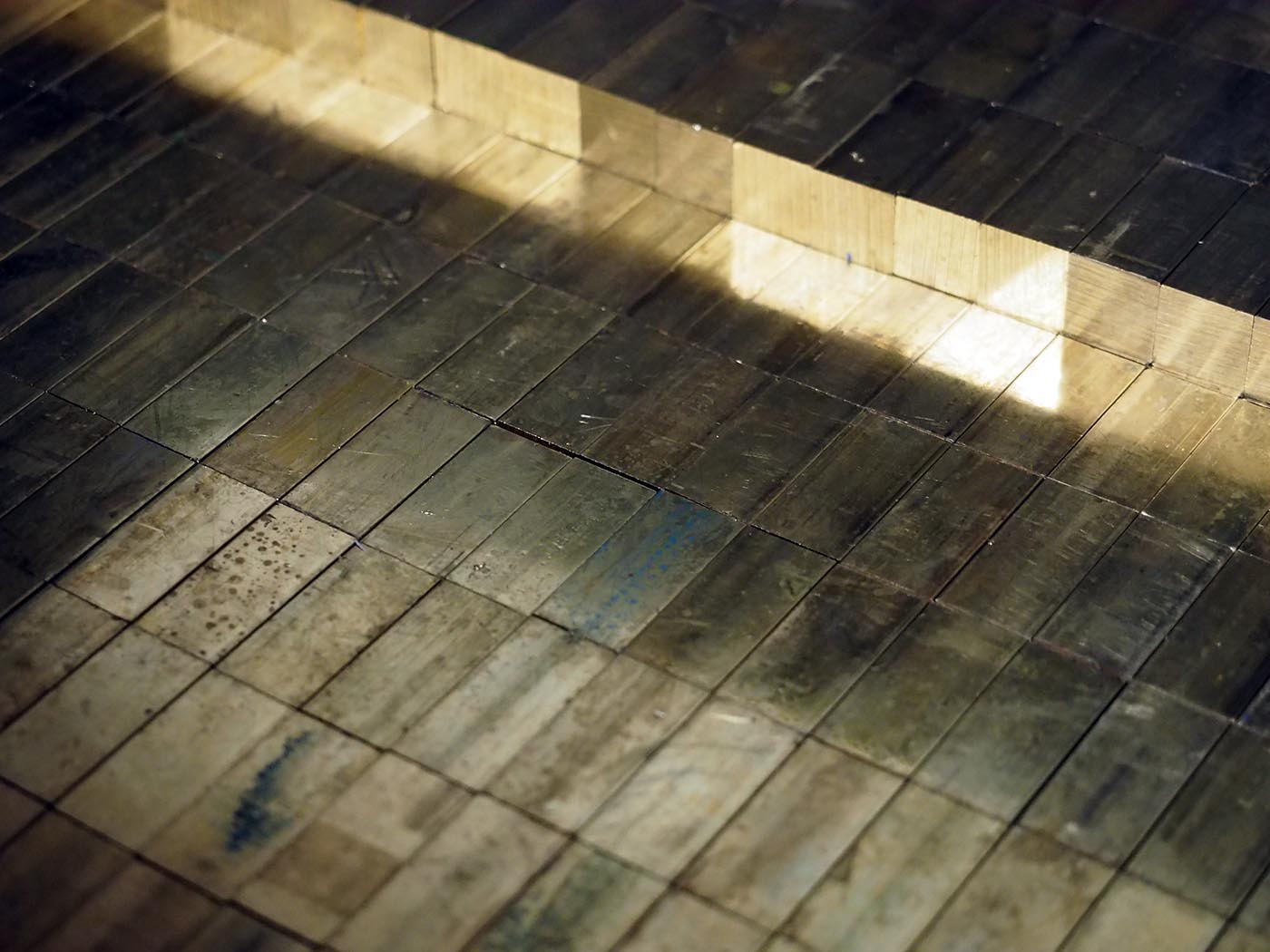
Material handling
Once the raw materials are sourced, how they are stored and handled has a major impact on their overall environmental impact. Certain chemicals and substances used in production processes may be harmless once they have been used, but leaks, spills and improper disposal can have huge impacts on the environment. Manufacturers located in North America, Europe and Japan are subject to the most stringent material handling regulations and the International Standards Organization (ISO) also takes material handling into account when it accredits a manufacturing facility. If a product is made in one of those locations or carries the ISO 9001 standard for quality control and 140001 standard for environmental impact ensures that you are buying a product that takes quality and the environment seriously.
Actual Manufacturing
Finally, we get to the meat and potatoes of what a manufacturer does. Make things! There are thousands of ways to make products and advances in technology are changing the game constantly. Tapmaster, for example, manufactures most of our components out of some sort of metal. We use low lead brass and stainless steel extensively in our products. There are many ways to make quality parts out of metal; casting, metal injection moulding (MIM), machining, extruding, stamping, and more recently even 3D printing. They each have their strengths and drawbacks. Casting and MIM have very high tooling costs and are often not easy to use for short run parts or prototypes. Stamping is extremely cost effective for parts made out of sheet metal.
The environmental impact of a process relies mainly on the energy input as well as the material waste. CNC machining can allow for extremely high part tolerances and flawless surface finishes, but the more material that must be cut away the more waste there is. Casting, MIM and 3D printing a part before machining the final surfaces can have significant positive impacts on material waste. For large production runs casting and MIM lead in per-part cost. But for smaller manufacturers like Tapmaster, 3D printing has opened up the material efficiencies of those methods without the inflexibility of tooling at 3rd party providers or the huge start-up cost for the facilities to undertake these processes.
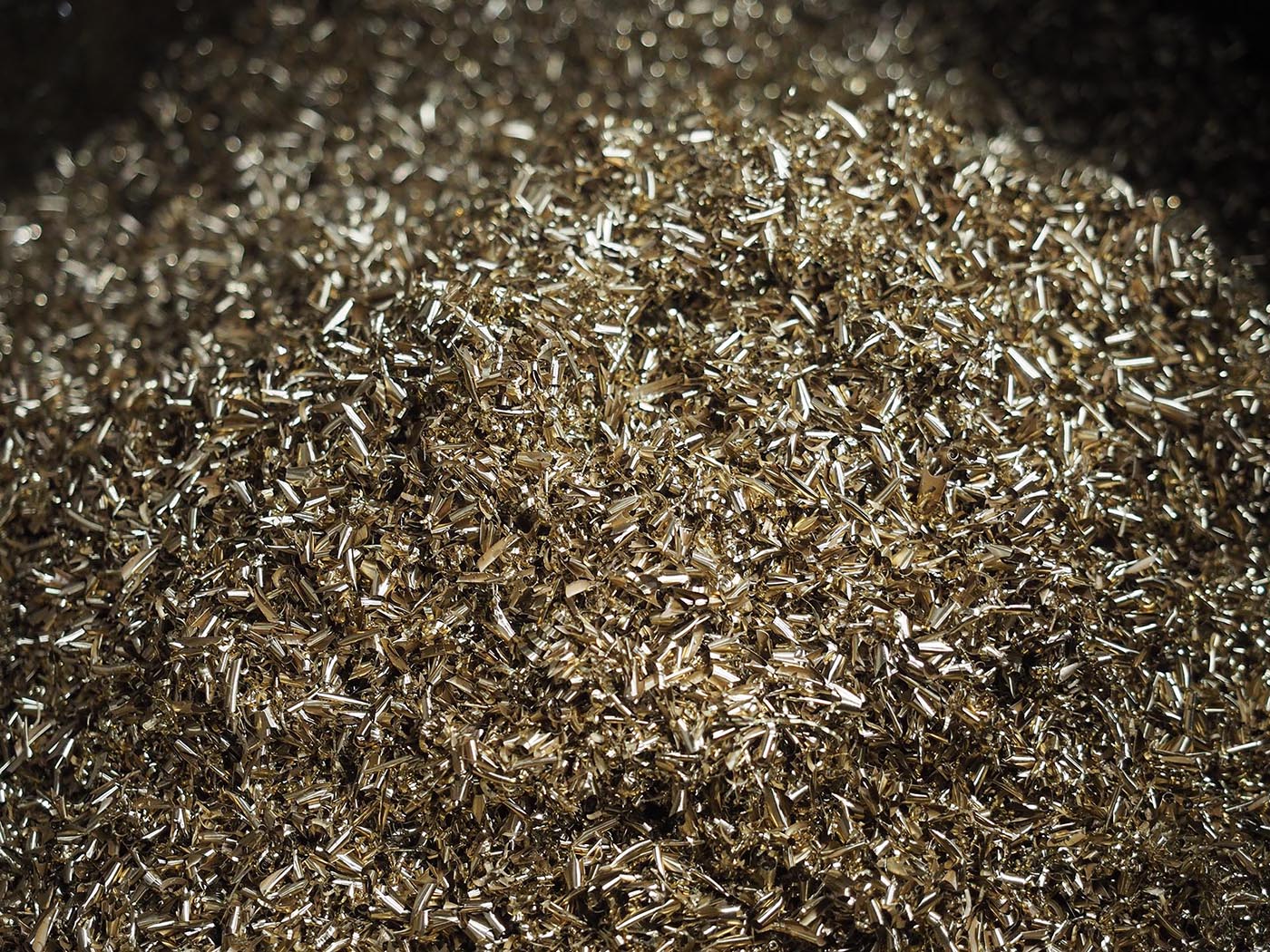
Packing and shipping
Once a product has been manufactured the final step that is in the control of the manufacturer is the packaging and shipping of products. Packaging provides a unique challenge for manufacturers. It must be robust enough to survive being shipped to the customer, while also minimizing the costs and environmental impact. Smaller boxes are cheaper to ship but might not offer enough protection for some items. Tapmaster has decided to go to a compostable formed pulp packaging that is made entirely of recycled paper product to provide the internal support needed to ensure safe arrival of our products. When compared to traditional plastic blisters or Styrofoam we find it provides equivalent or better protection while costing only slightly more money. Being compostable paper eliminates the risk of plastics finding their way into waterways and makes our packaging nearly 100% compostable/recyclable.
Shipping methods and distance also play a major role in the energy expense of getting a product to market. Trains and trucks are significantly lower impact than air freight. Manufacturing the final product in North America allows us to reduce shipping distances when compared to products made overseas.
Final thoughts
Ultimately, there are plenty of things that any manufacturer can do to minimize the impact of their process on the environment. Minor changes in a process can net large benefits for our planet. Some of the easiest and lowest-cost options are moving to paper-based packaging and scheduling supply shipments to take advantage of rail, trucking and shipping rather than rushed air freight. Other things like local material sourcing and manufacturing can be difficult for large companies or companies with established overseas supply chains and factories. However, with global supply chain issues causing massive delays in getting materials from overseas factories many companies are actively exploring the advantages of on-shoring at least part of their critical supply chain again. At Tapmaster we think that’s great!